How to avoid delays due to high volume orders?
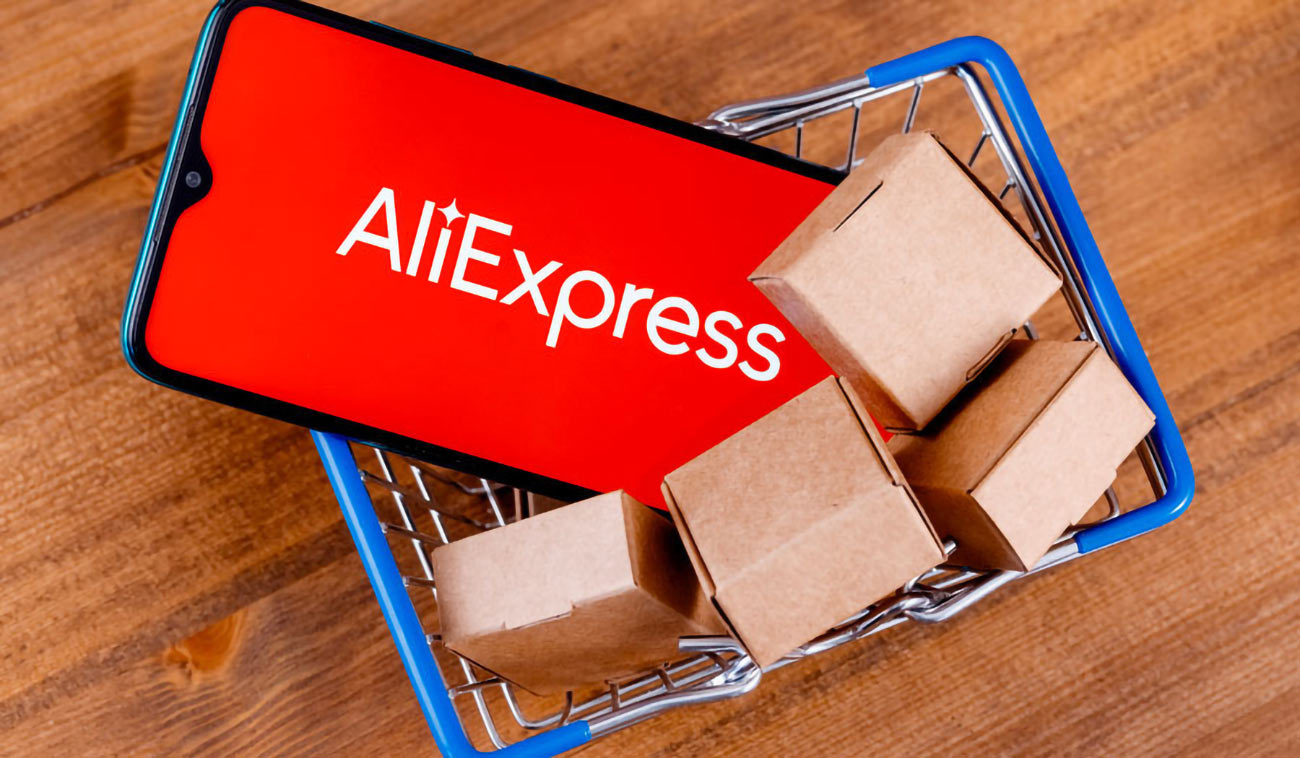
Running a business can often feel like a high-stakes juggling act. With growing consumer demand, the risk of delays due to high volume orders can loom large. It’s crucial for businesses, both large and small, to streamline their processes to not only cope with but also thrive during peak periods. In this article, we will explore effective strategies for avoiding delays caused by surges in order volume, ensuring that your business remains agile and capable of fulfilling customer expectations.
Understanding the Causes of Delays in High Volume Orders
Before diving into strategies to mitigate delays, it’s important to understand what commonly causes these bottlenecks. Here are some primary factors:
- Insufficient Inventory: High demand can quickly deplete your inventory, leading to delays in fulfilling orders.
- Poor Supply Chain Management: A lack of effective communication with suppliers can result in longer lead times when restocking items.
- Inadequate Staffing: Insufficient personnel during busy periods can hinder order processing and fulfillment.
- Outdated Technology: Relying on older systems can slow down order processing and tracking.
By identifying these factors, businesses can proactively implement solutions to prevent delays and enhance overall efficiency.
Strategies to Avoid Delays Due to High Volume Orders
Optimize Inventory Management
Efficient inventory management is fundamental in preventing delays. Here are actionable steps to enhance your inventory practices:
- Implement a Real-Time Inventory Tracking System: Use modern software solutions to maintain accurate inventory levels, enabling you to anticipate shortages ahead of time.
- Utilize Inventory Forecasting: Analyze historical sales data to predict future demand trends, allowing you to stock up before a high-volume surge.
- Establish Strong Supplier Relationships: Communicate with suppliers about your business cycle and expected demand to ensure that they can meet your needs in a timely manner.
Enhance Order Processing Systems
Streamlining your order processing can significantly reduce delays. Consider the following:
- Automate Order Processing: Investing in automation tools can help speed up the order fulfillment process, minimizing human error and accelerating dispatch times.
- Implement a Warehouse Management System (WMS): A WMS can optimize picking, packing, and shipping processes, making your operations more efficient.
- Use Barcoding and Scanning Technology: This technology simplifies inventory management and order accuracy, ensuring speedy processing of orders.
Upgrade Technology and Infrastructure
Modern technology can make a world of difference in handling high order volumes. Focus on:
- Investing in E-commerce Solutions: Ensure your online store is equipped to handle increased traffic and orders seamlessly.
- Utilizing Cloud Computing: Cloud-based solutions can provide flexibility and scalable resources during peak times.
- Enhancing User Experience: A well-designed interface can lead to smoother transactions, reducing cart abandonment and processing time.
Improve Customer Communication
During high volume periods, effective communication is paramount. To keep customers informed and satisfied, consider these strategies:
- Regular Updates: Keep customers informed about their order status through automated emails or SMS notifications.
- Establish Clear Policies: Clearly communicate shipping times and return policies to manage customer expectations.
- Offer Customer Support: Provide an easily accessible customer support service to address inquiries and resolve issues promptly.
Scale Your Workforce Accordingly
Having the right personnel during peak times is vital. Here’s how you can prepare:
- Hire Seasonal Staff: Consider bringing in temporary staff to help manage increased workload during busy periods.
- Provide Adequate Training: Ensure all employees are well-trained in their roles, allowing them to work efficiently even under pressure.
- Foster a Positive Work Environment: A motivated team can significantly contribute to improving operational efficiency during high-volume periods.
Implement Flexible Shipping Strategies
Shipping can be a major bottleneck during high order volumes. Here are some ways to improve your shipping process:
- Partner with Multiple Carriers: Collaborate with various shipping carriers to ensure you can meet demands without delays.
- Utilize Fulfillment Centers: Consider third-party logistics (3PL) services that can handle storage and shipping, allowing you more flexibility.
- Offer Diverse Shipping Options: Provide customers with multiple shipping methods, including expedited choices, to enhance satisfaction.
Real-Time Monitoring and Adjustment
Staying agile during high-volume periods is essential. You can achieve this by:
- Setting Up Key Performance Indicators (KPIs): Track metrics such as order processing times, inventory turnover, and customer satisfaction rates to identify areas for improvement.
- Using Analytics Tools: Tools that provide insights into order patterns and consumer behavior can help you adjust strategies in real-time.
- Soliciting Customer Feedback: Engage customers to gather feedback on their experience and adjust operations accordingly.
The Importance of a Proactive Approach
Being proactive rather than reactive is crucial in a high-demand environment. Here’s how you can foster a proactive culture:
- Conduct Regular Training Sessions: Continuous education can help staff adapt to changes and improve service delivery.
- Plan for Peak Seasons: Anticipate busy periods based on historical data and prepare your resources in advance.
- Regularly Review Processes: Ensure your business processes are continually refined for better performance and efficiency.
Leveraging Technology for High Volume Demand
In today’s digital age, harnessing technology can streamline operations and minimize delays. Consider the following:
- Adopt an Omnichannel Strategy: Integrate your sales channels to ensure customers have a seamless shopping experience, whether online or in-store.
- Utilize Chatbots: Implement chatbots to provide instant customer service and facilitate faster communication.
- Explore Machine Learning: Machine learning can enhance forecasting accuracy, allowing for better inventory management and order fulfillment.
Creating a Resilient Supply Chain
A strong supply chain can significantly reduce delays. You can achieve this by:
- Diversifying Suppliers: Relying on multiple suppliers can mitigate risks related to shortages and delays.
- Establishing Emergency Protocols: Create contingency plans to address unforeseen disruptions in your supply chain.
- Building Long-Term Relationships: Strengthening partnerships with suppliers can provide better service and prioritize your business during high volume seasons.
Conclusion
Implementing these strategies can significantly help in managing high volume orders and minimizing delays. By focusing on proactive planning, effective communication, and leveraging technology, your business can not only avoid operational bottlenecks but also improve customer satisfaction and loyalty. Embrace these practices and watch your business thrive during peak seasons.
LINK:
High volume orders can often lead to delays, impacting customer satisfaction and business efficiency. To mitigate these challenges, it is essential to implement strategic planning and adaptable workflows. Establish systems for effective inventory management, invest in automation tools for order processing, and ensure strong communication with suppliers. By anticipating peak periods, optimizing logistics, and maintaining flexibility in operations, businesses can successfully navigate high demand scenarios. Remember, a proactive approach helps in maintaining reliability, ensuring customers receive their orders promptly, which ultimately boosts your brand reputation and sales.
FAQ
1. What are the best ways to forecast high volume orders?
Implementing analytical tools that assess previous sales data helps in predicting high volume periods. Employ demand forecasting software that utilizes historical trends and market insights to gauge future orders. Additionally, stay in close contact with customers and suppliers to anticipate spikes in demand due to seasonal events or promotions.
2. How can inventory management help prevent delays?
Strong inventory management allows businesses to maintain optimal stock levels, reroute supplies as necessary, and quickly fulfill orders. Using automated inventory systems helps in tracking stock in real-time, ensuring that you can manage orders efficiently without overstocking or running out of critical items during high demand.
3. Should I consider outsourcing to handle high volume orders?
Outsourcing can be a viable solution for handling increased order volume. By partnering with fulfillment centers or third-party logistics providers, you can leverage their expertise in managing high volumes and distribution, allowing you to focus on core business aspects while ensuring timely deliveries.
4. How vital is communication with suppliers during peak times?
Maintaining clear and open communication with suppliers is essential during peak times. This facilitates timely orders, adjustments to inventory levels, and addressing any potential supply chain issues. Establishing strong relationships with suppliers can help you secure your stock and prioritize your needs during busy periods.
5. Can technology help in avoiding delays with high volume orders?
Absolutely! Implementing technology like automated order processing systems, warehouse management solutions, and customer relationship management software can streamline operations. These tools improve efficiency, reduce human errors, and provide real-time data, helping businesses respond quickly and allocate resources adequately during peak periods.